——————————————— ◆ Exhaust gas analysis ◆ ———————————————
Feed waste gas composition
(1) the odor concentration of fish meal and fish pulp which are widely used in the production of aquatic products and pet feed is related to the fish species, growth environment, freshness during processing, processing method and storage method. From the storage bin to the feed factory, this kind of material will undergo a certain degree of qualitative change. The result of qualitative change is that the fish body protein dissolves into various amino acids, and then it produces sulfur compounds, ammonia, biogenic amines, organic acids, etc. through the action of bacteria. These substances have a strong odor.
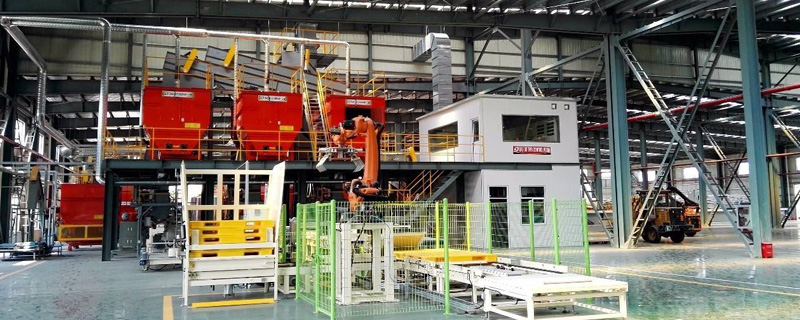
(2) in addition, fat, oil and food waste will also produce bad smell. At present, there is no effective control of odor pollution in feed processing plants in China. The odor of feed factory is generated in the conveying, mixing and forming section as well as the dust. Therefore, the odor control must be considered together with the dust control to achieve the dual purpose of removing odor and controlling dust.
——————————————— ◆ Technological design ◆ ———————————————
Process Brief
(1) after the dust and granular substances are removed by pretreatment, the waste gas is sent to the activated carbon adsorber I and II. When the activated carbon adsorber I is close to saturation, the treatment gas is automatically switched to the activated carbon adsorber II (the adsorption operation of the activated carbon adsorber I stops), and then the activated carbon adsorber I is desorbed and desorbed with hot gas flow to desorb the organic matters from the activated carbon. In the desorption process, the organic waste gas has been concentrated, and the concentration has increased dozens of times than before, reaching more than 2000 ppm. The concentrated waste gas is sent to the catalytic decomposition unit, and finally discharged as CO2 and H2O.
(2) after the desorption, the activated carbon adsorber I will enter the standby state. When the activated carbon adsorber II is close to saturation, the system will switch back automatically, and at the same time, the activated carbon adsorber II will be desorbed and desorbed, so it will work in cycle.
(3) when the concentration of organic waste gas reaches more than 2000 ppm, the catalytic bed can maintain spontaneous combustion without external heating. The scheme not only greatly saves energy consumption, but also reduces equipment investment because the treatment capacity of catalytic decomposer only needs 1 / 5 of the original waste gas treatment capacity (60000m3 / h). This scheme is not only suitable for continuous work, but also suitable for intermittent work.
——————————————— ◆ Cooperation ◆ ———————————————
Process Brief
(1) after the dust and granular substances are removed by pretreatment, the waste gas is sent to the activated carbon adsorber I and II. When the activated carbon adsorber I is close to saturation, the treatment gas is automatically switched to the activated carbon adsorber II (the adsorption operation of the activated carbon adsorber I stops), and then the activated carbon adsorber I is desorbed and desorbed with hot gas flow to desorb the organic matters from the activated carbon. In the desorption process, the organic waste gas has been concentrated, and the concentration has increased dozens of times than before, reaching more than 2000 ppm. The concentrated waste gas is sent to the catalytic decomposition unit, and finally discharged as CO2 and H2O.
(2) after the desorption, the activated carbon adsorber I will enter the standby state. When the activated carbon adsorber II is close to saturation, the system will switch back automatically, and at the same time, the activated carbon adsorber II will be desorbed and desorbed, so it will work in cycle.
(3) when the concentration of organic waste gas reaches more than 2000 ppm, the catalytic bed can maintain spontaneous combustion without external heating. The scheme not only greatly saves energy consumption, but also reduces equipment investment because the treatment capacity of catalytic decomposer only needs 1 / 5 of the original waste gas treatment capacity (60000m3 / h). This scheme is not only suitable for continuous work, but also suitable for intermittent work.