The company attaches great importance to environmental protection while vigorously improving the economic benefits of the enterprise and paying attention to product quality. The company leaders, in line with the principle of creating a good production and living environment for the employees and the surrounding residents, collect and deal with the waste gas generated in the operation process and completely eliminate the hidden dangers of the enterprise's development. Entrusted by the company, shandong baolan environmental protection engineering co., LTD. Based on the design principle of mature and reliable technology, reasonable overall layout, convenient operation and management, and low processing cost, we have compiled this scheme.
According to the operational cost and safety of the waste gas treated in this project, the process route of this project adopts "activated carbon adsorption desorption + ionization trap" as the core process to treat the waste gas of this project. The process route diagram of the project is shown in the figure:
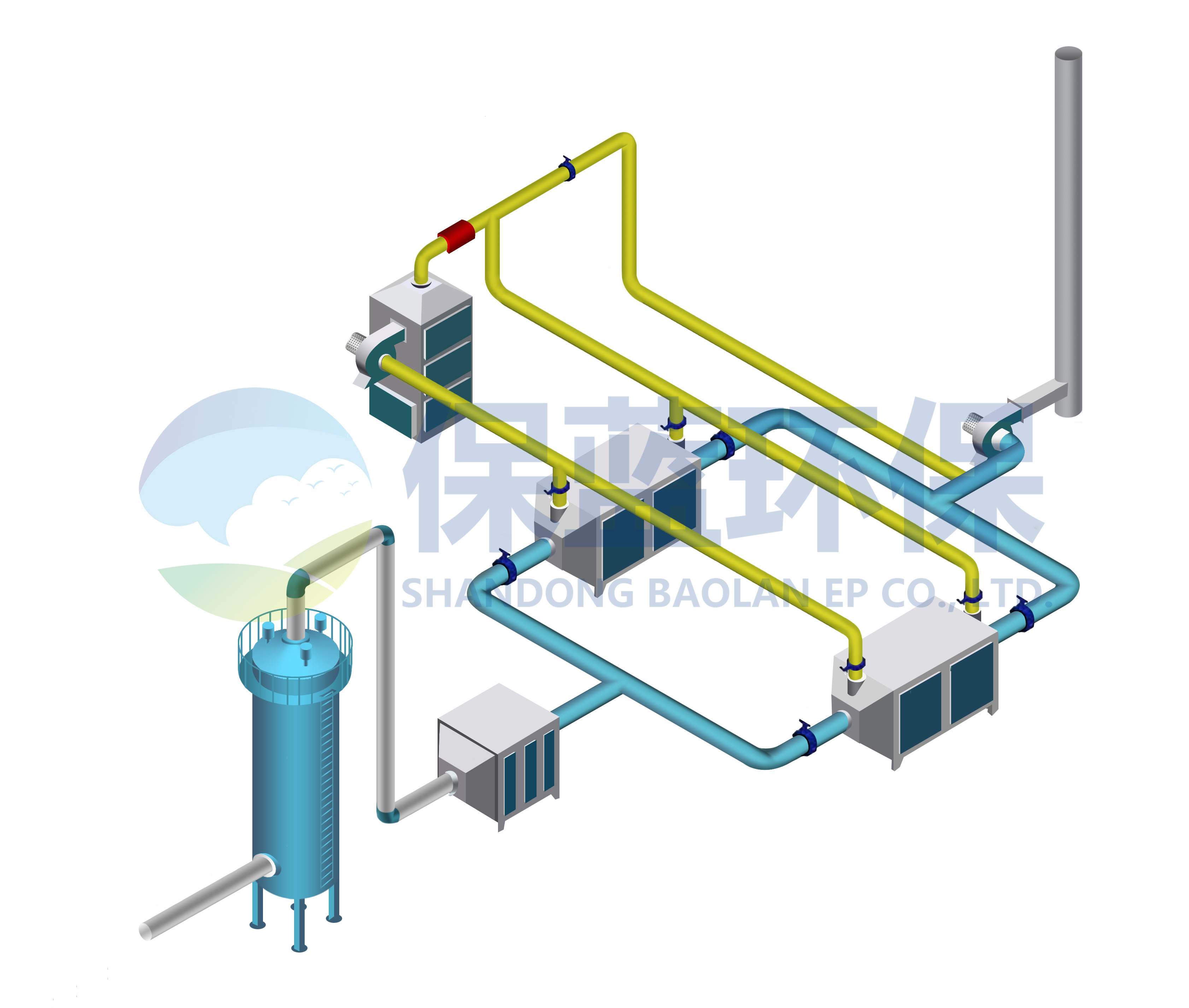
Process analysis:
As a first step, after collecting the waste gas into the ionization trap, when the waste gas by the dust and tar material in the exhaust gas in charge under the action of ionization, to charge with wire and tube wall motion, and loss of charge, when the adsorption on precipitation in the miscellaneous quality increases to greater than its adhesion, under the action of gravity, automatically downflow, capture from ionization bottom discharge, net gas from ionization trap upper left and into the next procedure, hence leading to the degradation of pollutants removal.
The second step is the process of adsorption concentration -- desorption and desorption -- catalytic decomposition. By 2 activated carbon adsorbers, 1 catalytic decomposer (auxiliary low pressure fan, valve, etc.). Exhaust gas after preprocessing to remove dust, granular material into activated carbon adsorber A and B, when activated carbon adsorber A close to saturation, will first deal with the gas automatically switch to the activated carbon adsorber B (activated carbon adsorber A stop operation), and then use thermal desorption of activated carbon adsorber A stripping, stripping off the organic matter from activated carbon. In the desorption process, the organic waste gas has been concentrated, the concentration is increased several times than the original, up to more than 2000ppm, the concentrated waste gas to the catalytic decomposition device, and finally become CO2 and H2O emission. After desorption and desorption, activated carbon adsorber A enters the waiting state, and when activated carbon adsorber B approaches saturation, the system will automatically switch back to desorption and desorption of activated carbon adsorber B, and so on. When the concentration of organic waste gas reaches above 2000ppm, the catalytic bed can maintain spontaneous combustion without external heating. This scheme not only saves a lot of energy consumption, but also reduces the equipment investment because the catalytic decomposer only needs 1/5 (60000m3/h) of the original waste gas treatment capacity. This scheme is suitable for both continuous work and intermittent work. The desorption and desorption of a single activated carbon adsorbent takes approximately 2-3 hours. The adsorption fan is controlled by a frequency converter and can be adjusted according to the required air volume or the net negative pressure at the inlet of the device.